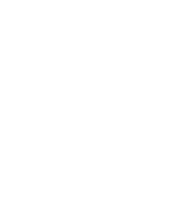
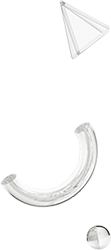
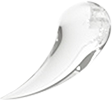
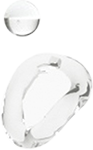

In Mould Labelling (IML): high-definition personalization by plastic injection moulding
In Mould Labelling, better known by itsabbreviation “IML”, is a personalization device for plastic injection molding. This technique combines industrial expertise in the manufacture of food packaging with tailor-made personalization techniques. This device combines unique aesthetics with the practicality of containers.
The IML personalization devices offered by Re-uz ® are a successful symbiosis of industrial know-how,plastic injection and design freedom.
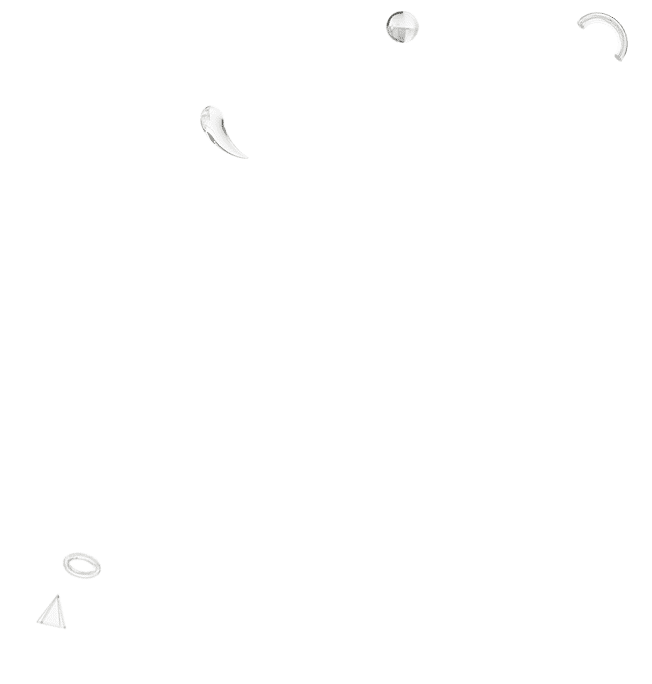
High-definition personalization injected into the walls of the container
IML is a decoration process in which the printed label is placed in the mold before the plastic is injected. This ensures perfect fusion between the label and the plastic material forming the walls of the container.
This personalization technique eliminates the need for subsequent labeling, providing a smooth, crease-free finish that’s resistant to heavy use and washing.
The major advantage of IML is the ability to fully customize the container. Customization is almost limitless: from the color palette to complex graphics, the possibilities are vast.
Precision industrial know-how at every stage of production
Industrial know-how therefore plays a crucial role. Re-uz ® masters both the design and manufacture of molds. It guarantees the exceptional precision inherent in every stage of production. Precise management of the plastic’s melting temperature, pressure and injection time are all parameters we control to obtain optimum results.
One-piece plastic injection molding produces lightweight, durable and aesthetically appealing containers. The polypropylene used guarantees increased impact resistance and responds to variations in container temperature (washing, oven, microwave, freezer) and content (hot or cold beverage).
Increased visibility on a customized container designed for reuse
IML personalization offers enhanced visibility. Every brand and every customer strengthens its reputation by associating it with a durable, useful and reusable container.
A real differentiator, personalized containers help to mobilize users in a reuse approach.
Combining the useful with the pleasurable to minimize plastic waste: end consumers will be more attracted by aesthetically pleasing and unique containers. They will convey both eco-responsibility values and those of the associated brand.
How does In-Mould Labelling & the manufacture of a Re-uz ® cup work?
1
Label design & printing
The decor is created in collaboration with the integrated graphics agency Re-uz ®. L’Anamorphosis is then established to coincide with the shape of the container to be manufactured. The label can then be printed on plastic film in high definition.
2
Label cutting & shaping
The label is then die-cut. Its atypical shape simply corresponds to the shape of the beaker. By bringing the two ends together, a flared cylinder is already visible… Thelabel fits snugly against the sides of the container.
3
Placing the label in the mold
Steps 3 and 4 are carried out at the same time. The label is sucked into the mold, curling millimetrically against the walls.
4
High-temperature plastic injection in the mold
The plastic is injected into the mold at high temperature. Only industrial machines can contain the pressure exerted at this stage of the manufacturing process. Plastic and label merge.
5
Cooling & removing the finished cup
The plastic cools and sets. The cup is then mechanically extracted from the machines. The customization rendering is exceptional.
how is labeling done in the mold?
After high-resolution four-color printing, the label is cut to fit the container.
The decoration is then positioned in the mold by "vacuuming" the label.
Theplastic injection process is carried out, then the cup is recovered.
What are the advantages of In-Mould Labelling for customizing a reusable cup?
Sustainable personalization on reusable containers
The personalized label merges with the walls of the container during the manufacturing process: decorations and information are truly embedded in the plastic. Thanks to this technique, there’s no need to affix adhesive labels (and no risk of scratches or damage): proven longevity.
Exceptional high-resolution customization quality
Prior to injection molding, the labels are shaped and printed in high resolution. Each container format is assigned a specific label shape to match its curves perfectly. This device allows the container to be decorated at 360°, giving an exceptional photo effect.
Tough as nails
Injected IML labels are just as waterproof as their associated containers. They areresistant to wide temperature variations. Containers and contents can be refrigerated or deep-frozen. The whole unit can be microwaved at temperatures of up to 110°C.
An undeniable ecological feature & proven recyclability
Printed labels are made from the same plastic materials as their containers (polypropylene film). Thiseco-design approach results in single-material products that are fully recyclable.
Exceptional handling & an unchanging decor
The label is not glued to the container, but integrated into it. The walls are smooth, making it impossible to remove or damage inlaid personalization. This device enables containers to be stacked without repetitive contact and/or friction damaging the decor.
Identical molds for customized production
Re-uz ® offers a wide range of containers. The Ecocup ® range is based on moulds that have been around for many years.
Each new custom-made container is similar in capacity, size and weight to those previously manufactured… Only the customization changes! As a result, they remain just as stackable and ergonomic as their predecessors.
A dedicated creative agency and committed partners
At the launch of an IML personalization project, the Re-uz ® graphics teams work with you to define your communication axis, and design and model the graphic aspect of your communication. This dedicated team knows all the ins and outs of successfully customizing a container to make every IML project a success.